How Property Risk Engineers help pharmaceutical companies supply vital medicines
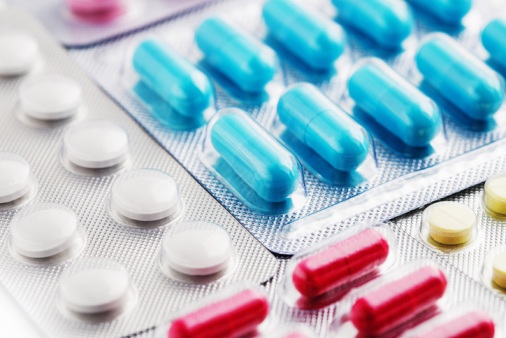
By AXA XL Risk Consulting Senior Risk Consultant Mark Driscoll
Pharmaceutical companies have a lot riding on the safe and successful operation of their facilities. Fires, floods, windstorms, power failures and other interruptions can jeopardize the production of thousands of vital medicines. Especially now with COVID-19 vaccine development in full swing, the health and safety of entire populations depend on the safety and security of pharmaceutical manufacturing.
These companies may have thousands of facilities worldwide, with millions of pieces of equipment. Incidents and interruptions will inevitably occur, but proactive exposure assessment and contingency planning can mitigate damage and minimize disruption.
AXA XL Risk Consulting provides loss prevention services to all clients to help them assess risks and implement loss control strategies. To help pharmaceutical companies protect operations, our risk consultants first sit down with risk managers to understand their business objectives, key locations and possible pinch points in their operations before planning onsite visits.
On-Site Risk Assessments
Risk consultants visit client sites to assess two key areas of exposure: administrative controls and physical deficiencies.
Administrative controls deal with the human element. How much care and control does a company exert over things like employee training, workplace safety protocols, enforcement of cleaning and sanitation procedures and maintenance schedules? Shortcomings in any of these areas may pose a risk to important equipment, valuable inventory, and critical business processes.
Management of on-site contractors is a major component of this category, as they often engage in high-risk activities like hot work. Risk consultants examine how well contractors are trained on company protocols, the adequacy of program documentation, and how those protocols are enforced.
Physical deficiencies may include substandard fire protection systems, lack of appropriate aisle spacing or other product storage issues, inadequate backup power sources, lack of flood protection strategies, old or faulty equipment, limited business continuity planning, etc.
Regular site visits help to spot and solve these problems early, minimizing loss potential.
Risk Control Implementation
After a thorough survey, risk consultants offer specific recommendations targeting a company’s weak spots and will help managers build out plans for implementation. Whether a client is also buying insurance through AXA XL or not, our team is always there to assist.
Some recommendations will be simple, like tweaking a training protocol or maintenance schedule. We offer hot-work training for contractors, for example, as well as division or account level corporate programs training. Other changes may demand more time and resources. Installing a new sprinkler system to meet National Fire Protection Association Standards, for example, is not typically a quick fix.
Risk consultants help facility managers prioritize recommendations and plan for improvements within their capital constraints. This could include helping them compile data to demonstrate ROI and build a case for a capital improvement request. It could also include helping them understand the technical specifications of a new piece of equipment, so they know exactly what to look for. Most facility managers, after all, are not technically competent in the many facets of automatic fire protection.
Some recommendations may take years to implement as priorities shift, new projects emerge and budgets take shape. Our implementation plans account for these scenarios and outline a strategy that is practical and realistic.
Involvement in Facility Selection and Design
Risk consultants also get involved in due diligence assessments of potential new properties, working with risk managers during facility selection and design phases to pinpoint vulnerabilities and suggest upgrades needed to begin production in a highly protected manner.
Our feedback provides another decision point in the acquisition process which may impact negotiations. At the very least, these assessments help operations and facility managers factor necessary improvements into the production timeline and budget. Proactively outfitting a facility with all the bells and whistles to minimize potential for loss is easier than retrofitting once production has started.
Unique Challenges of COVID Vaccine Production
The primary challenge pharma companies faced during COVID vaccine development was a compressed timeframe. The speed needed to retrofit facilities and get new production lines up and running was unprecedented.
Storage requirements presented another obstacle. Certain COVID vaccines require ultra-low storage temperatures of approximately -90 degrees Fahrenheit. While cold storage in general is nothing new for the pharmaceutical industry, these extremely low temperatures exceeded what existing and typical refrigeration capabilities could handle.
Manufacturers were tasked with finding new spaces that could accommodate freezer farms – and deliver enough power to maintain such low temperatures. Vaccines may only last for 36 to 48 hours once out of refrigeration, so having backup power is essential.
Months before production even began, risk consultants were on site helping companies implement new assets and facilities and identifying protections needed to ensure safe and reliable operations.
This is where longstanding relationships and transparent communication come into play.
It’s absolutely vital for risk consultants to be viewed as valued partners in risk mitigation. Our risk consultant team meets with top pharmaceutical clients on a weekly basis to discuss high-capital, high-risk projects. At the site level, we have well-established relationships with facilities managers. They know to involve us in early design phases to incorporate our input to project scope.
Thanks to that high level of communication, manufacturing and storage facilities were ready to go as soon as vaccine clinical trials were complete and approvals granted. And while COVID vaccines brought some unexpected challenges, they likely won’t be the last therapies to demand such quick turnaround times.
Staying in constant contact and maintaining strong relationships ensures our team is aware of changing plans, on top of new demands and ready to jump in, no matter the timeline.
What’s Next?
New and ever-changing technology is giving risk managers and risk consultants opportunities to boost loss prevention even further. We can stay connected, track products from every step in the supply chain, collect data in real-time to catch potential exposures before a costly loss occurs, and more.
This year, for example, AXA XL Risk Consulting launched Digital Risk Engineer, a service which uses Internet of Things technology to monitor the health of your assets and buildings around the world remotely. An easy-to-install device is integrated seamlessly within a facility to capture real-time data from connected systems such as energy, water, heating, ventilation, and air conditioning (HVAC). The data and insights are accessible to our clients and our risk consultants via an online dashboard to help us detect any potentials issues early on.
Similarly, Risk Scanning provides a fast overview of a client’s exposure by region, country, or peril so that risk managers can make decisions to optimize their loss prevention measures and investments. Based on closed questions asked to risk managers through a digital application, and external data, we are now able to analyze, by weighting the different risk variables, the probability of risk incidence, and then propose actions and protection recommendations to mitigate the risks.
No doubt, more adoption of new technology, greater connectivity, and trusted relationships with loss prevention experts will continue to play a big role in helping the pharma industry tackle property exposures and more importantly, helping them address issues that might stand in their way of supplying critical medicines when they are needed most.
About AXA XL
AXA XL is the P&C and specialty risk division of AXA which provides property, casualty, professional and speciality products to industrial, commercial and professional firms, insurance companies and other enterprises, here in the UK and throughout the world. With underwriting teams based in the US, UK, EMEA and Asia Pacific regions, we can make decisions close to the markets you serve and work with you to tailor cover to your business needs.
We help businesses adapt and thrive amidst change. Rather than just paying covered claims when things go wrong, we go beyond protection into prevention so your business can go beyond the unexpected.